Manufacturing Top-Quality Medical Devices with a Digital Touch
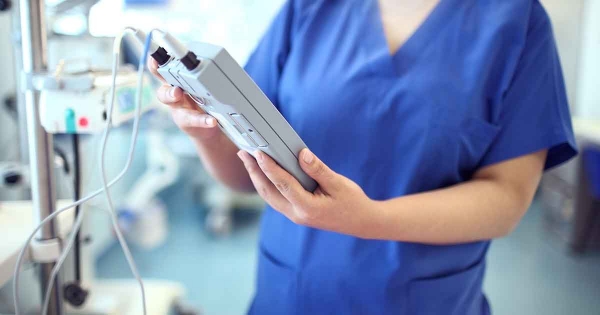
Can you think of a human trait that hasn’t evolved? For me, that would be our inherent resistance to new ideas.
Let’s take the case of X-ray, the best available method of identifying bone fractures till date. When Wilhelm Conrad Röntgen discovered the X-ray in 1895, most people didn’t take it seriously. The New York Times referred to this public disbelief by mockingly calling it the “alleged discovery of how to photograph the invisible”.
Interestingly, the negative reception surrounding new concepts has never managed to stifle curiosity and innovation. The technology behind the large-scale production of medical devices has continued to upscale and evolve in an attempt to make life easier and simpler for manufacturers. The latest addition being digitalization.
Giving Medical Device Quality a Real-Time Boost
Digitalization is changing operations and manufacturing across industries, fostering new levels of efficiency and innovation in sectors like healthcare device manufacturing. The regulatory compliance and product quality requirements in these industries have however been inhibitors to this digital revolution owing to the validation efforts and risks associated with implementing new technologies in a regulated environment. That being said, the industry can no longer stick to age-old conventions at the cost of losing out on the benefits that digitalization promises to deliver. At the end of the day, technology has to be aligned to medical device manufacturing processes to curb validation efforts while maximizing value.
Real-time data can empower manufacturers to stay on top of product quality. Data generated from embedded IoT sensors can also facilitate the analysis of equipment performance on a real-time basis. This can in turn drive better quality control on processes and greater visibility into ‘Critical to Quality’ parameters. Using Big Data for informed decision making can generate $100 billion in revenues annually for the US healthcare system by improving clinical trials and research, fueling innovation, and building advanced tools for consumers, insurers, physicians, and regulators.
3D Printing–Simplifying Quality Compliance
Intensive medical procedures like facial reconstruction, prosthetics and implants require a high level of precision and personalization. This is where 3D printing is creating a difference by offering manufacturers the liberty to craft high-quality medical equipment at relatively lower costs.
Prosthetics is often an expensive affair for patients, with units costing up to $100,000. This is where 3D printing can do wonders. Recently, a non-profit organization implemented advanced 3D printing to develop open-source prosthetic hands priced under $1000.
By using 3D printing and adapted medical materials in tandem, medical equipment manufacturers can also create intricate medical implants. Recently, a Melbourne-based medical device manufacturer designed and developed a 3D printed sternum and rib cage for a patient who was suffering from chest wall sarcoma. This particular chest section was difficult to recreate with conventional prosthetics. The surgical team chose not to compromise on the quality of the implant by resorting to 3D printing.
Both versatility and quality assurance make 3D printing a preferred method for designing and developing applications around medical devices, biologics, and drugs. This unique concept also enables medical device manufacturers to make changes to a particular equipment, eliminating the need for an additional setup.
Where’s Medical Device Manufacturing Heading?
Device recall issues have long been a major concern for the medical device manufacturing industry. Regulators have responded to such incidents by tightening existing guidelines and adding new ones as and when required.
Going forward, as industry players face more pressure to meet standards pertaining to quality, traceability, and compliance, digitalization will offer them the biggest edge over their competitors. Next-generation manufacturing execution systems (MES) for instance, can help eliminate errors even before they occur. A fully integrated MES unites all parts of a plant through a common information exchange platform to optimize equipment availability, order scheduling, and machine capacity. It further offers device manufacturers with an intuitive view of the overall plant floor so that they can stay abreast of the status of all processes, machines, and product batches.
Companies need to eradicate paper records and start using real-time insights to eliminate process and product errors, and infuse quality into product lines themselves. Medical device manufacturing plants that fail to recognize the importance of digitalization today will find it very difficult to compete tomorrow. When it comes to implementing latest technologies, the early bird always gets the worm!