Highlight
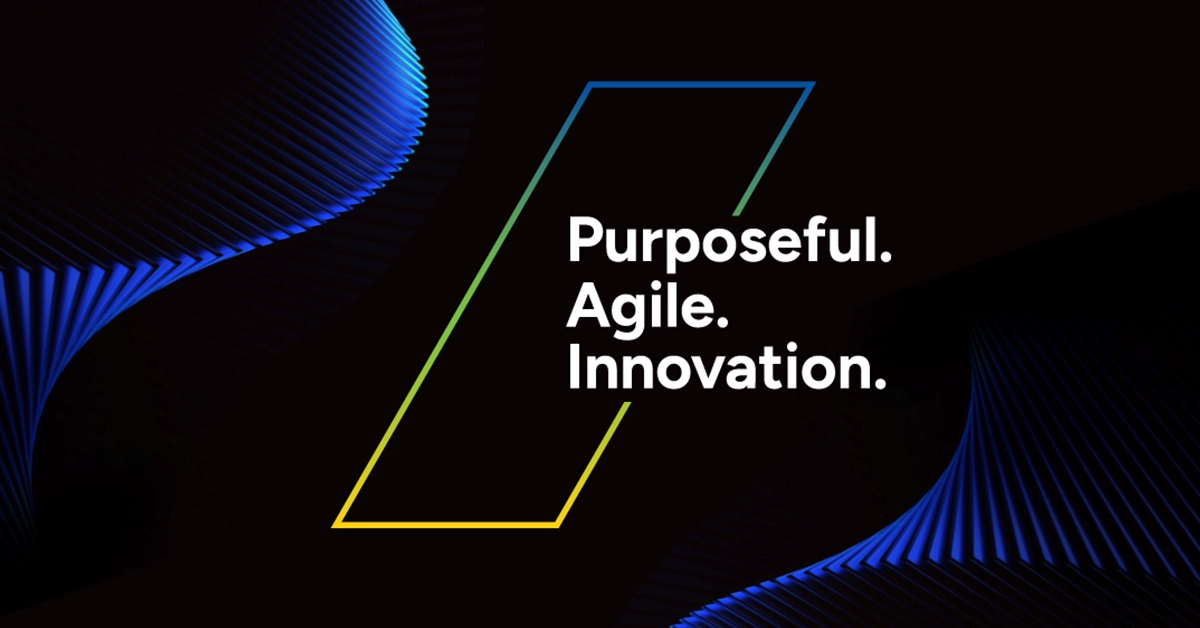
Purposeful. Agile. Innovation.
The shifting patterns of migration have a profound impact on global economic dynamics, driving the emergence of a new middle class. This transformation demands a re-evaluation of solutions and product...
Latest Reads
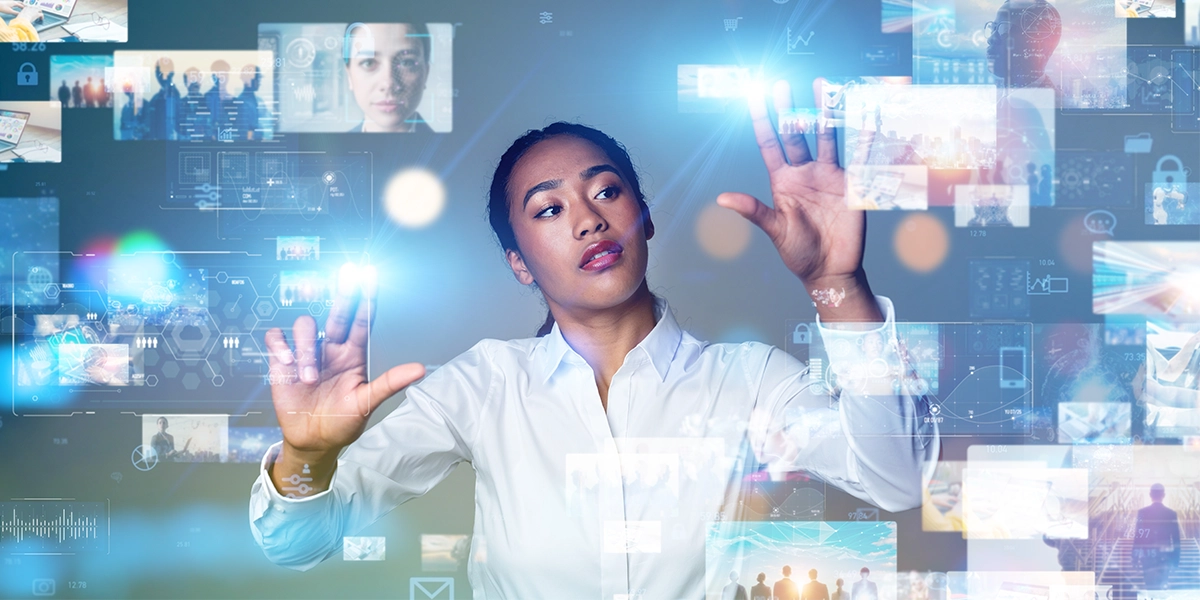
- Media & Entertainment
Unlocking the Power of Private CDNs in the Media and Entertainment Industry
by Anshuman